工业质检3天变3小时!第三方LIMS击破数据孤岛困局
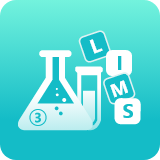
第三方检测实验室LIMS
白码LIMS实验室管理系统,主要服务于第三方检测机构、企业内部研发型实验室、内部质量检测实验室。主要服务行业包括,水利,环境,交通,建筑,芯片,水产,电子电器,电力工程。
工业制造实验室是产品质量的核心防线,却常陷入“数据孤岛”的泥潭。原材料检验、过程监控、成品检测数据分散在不同系统、设备甚至纸质记录中。华南某大型机械厂曾因热处理车间金相数据与装配线性能测试报告割裂,导致批次质量问题追溯耗时72小时,损失超150万元。
数据孤岛引发的三重危机:
● 追溯链条断裂: 某汽车零部件厂原材料成分报告与最终疲劳测试结果无法关联,问题定位延迟48小时,产线被迫停摆
● 资源严重浪费: 35%的工业实验室存在重复检测,仪器利用率不足60%,源于历史数据无法复用
● 合规风险失控: 审核时需人工拼凑分散数据,某电机企业CNAS评审因“检测数据完整性不足”被开具不符合项
一、孤岛丛生:工业检测数据的现实困境
工业制造检测链条长、环节多、设备杂。从金属材料的成分光谱分析,到组装后的振动测试,数据产生于数十类仪器、多个车间、不同系统。这些数据往往各自为政:
● 设备协议壁垒: 老式拉力机、新型三坐标仪等设备通信协议各异,数据自动采集率不足40%
● 系统互不相通: ERP的生产批次信息与LIMS检测任务脱节,质检员需手动匹配,错误率超15%
● 车间信息滞后: 现场工艺参数变更(如注塑温度调整)无法实时同步至实验室,检测标准依据失效
二、第三方LIMS的破局之道:构建全域数据枢纽
工业制造行业第三方lims系统推荐的核心价值在于打破壁垒,实现检测数据的统一治理与智能联动。
(一)全域数据融合引擎
● 四维设备直连: 通过协议解析(Modbus/OPC)、数据库对接、串口通讯、AI视觉识别,实现99%工业设备数据自动采集。某轴承厂接入67台老旧设备,数据获取效率提升300%
● 多系统无缝集成: 与MES生产执行系统、ERP资源系统深度对接,自动关联生产工单与检测任务。长三角某装备企业借此消除批次信息手工录入,错误归零
● 物联网实时同步: 车间传感器数据(温湿度/压力值)自动推送至LIMS,触发关联检测项动态调整。如铸造车间温度超标时,系统自动追加材料金相复检
(二)数据智能驱动决策
工业制造行业第三方lims系统推荐以数据流重构质检流程:
1. 全链路追溯视图: 输入产品序列号,一键展示从原料入厂检验到成品出货测试的全维度数据图谱,追溯时效从3天压缩至10分钟
2. 动态预警机制: 当过程检测数据偏离历史模型(如焊接强度波动超5%),系统自动触发预警并冻结关联批次,某重工企业拦截质量事故23次
3. 资源优化配置: 基于历史检测负载与设备状态,智能分配任务。珠三角电子厂仪器利用率从58%提升至89%,检测周期缩短40%
三、转型实效:从信息碎片到决策中枢
案例:威达精密制造(苏州)有限公司
该企业原有12套独立数据系统,质量问题平均定位耗时51小时。
部署第三方LIMS后:
● 数据整合突破: 接入5类生产系统、142台检测设备,构建唯一数据源,报告生成速度提升5倍
● 质量成本锐减: 重复检测率下降68%,质量问题追溯时效压缩至3小时,年节省成本超280万
● 决策精度跃升: 通过历史数据建模预测产品失效点,客户退货率降低42%
华北某机车制造商则实现跨基地数据协同:三大分厂检测数据实时汇聚总部平台,质量问题根因分析效率提升90%。评审时一键调取全流程电子记录,CNAS不符合项减少75%。
工业制造行业第三方lims系统推荐应注重异构集成能力与工业场景适配性。白码第三方LIMS系统针对工业数据痛点,其实验室电子记录本(ELN) 模块彻底替代车间纸质记录,实现检测数据自动运算与实时同步;可视化大屏则集中监控多分厂检测进度与设备状态,异常数据10秒预警。系统已助力威达精密等企业实现数据追溯效率提升600%、质量决策周期缩短85%。对于亟待打通数据链的工业实验室,白码提供从设备连接到智能分析的一体化数据治理方案。